
RANARCH
Hi ! I am Rana Al Rawi
Over the years, I’ve had the opportunity to work on a number of incredible projects that have allowed me to grow and establish myself within the architectural field. I hope you’ll enjoy viewing my projects as much as I enjoyed working on them. Go ahead and explore, please don’t hesitate to reach out if you’d like to learn more.
CROSLAND CHROMA
GOERGIA TECH - CAMPUS LIBRARY BUILDING
Atlanta, GA | Formations Studio
Worked on the design phase of this unique project located at the roof top of the Georgia Tech campus Library with Tristan Alhadad, the director of Formations Studio.
Crosland Chroma meant to act as both a public art /sculptural piece as well as a safety barrier for the students. Crossland Chroma is a series of vertical fins that twist themselves 90 degrees to create an incredible spectrum of colors across the entire roof top space during the day and night. Pictures from the opening day 03_30_2022.
5th Year Studio | Department of Architecture | Kennesaw State University
The project was an exploration to develop the blending of computing and the physical realm. This Prototype model is designed with elements “pixels” that extrude perpendicularly from the surface of the wall to create a variety of configurations. By controlling the movement of each pixel through the application of Arduino and Grasshopper, the pushing and pulling mechanism in response happens horizontally to serve social, environmental and interactive purposes.
DYNAMIC PIXELATION
Dynamic Environment | Focus Studio
Professor Mostafa Alani
The implementation of each pixel is designed according to the official ergonomic standards set by Allsteel.com to best provide people with comfortable spatial interaction. Therefore, the initial shapes selection for the pixels and dimension processes
started with a consistent grid system followed by an ergonomic study to determine functions like sitting, lounging, inhabiting and interacting with the wall. This kinetic pixilation system will be divided into two different categories based of their reaction accordingly: Responsive and Interactive.

![]() | ![]() | ![]() | ![]() | ![]() |
---|---|---|---|---|
![]() | ![]() |
POST-WAR LEARNING ENVIRONMENTS
REDEFINING SCHOOLS DESIGNS IN IRAQ
The learning environments in Iraq have been greatly affected by war and ongoing conflict in the past two decades. As a result, the drop-out rates have increased, academic achievement is low, and the students are suffering from stress. Architecturally, the existing school typologies in Iraq were designed more than 70 years ago and does not reflect the needs of the 21st century students.
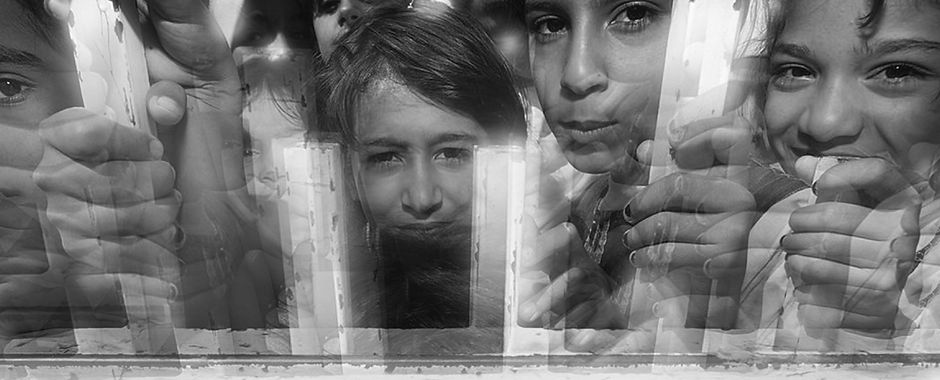
Thesis Research | 5th Year Studio
Department of Architecture | Kennesaw State University
Professor Giovanni Loreto
For as long as I can remember, school has been an integral part of my life. I was the kid who woke up every morning eager to get to school. At that time, I was living in Iraq where the learning environments have been greatly affected by war and ongoing conflict in the past 2 decades.
Going back five years ago when I began my study in architecture, I got the opportunity to start working as a teacher. I realized that I am studying to become an architect but I will always be passionate about teaching children, and truly enjoyed doing both. From this perspective, when I start thinking about my thesis project, I recognized an amazing opportunity to not only learn from the experience I had as a student in my home country or from my job as an educator, but also to tackle a real problem through the medium of architecture.

Annual KSU Cooper Carry
3MT Architecture Thesis Competition
Thesis Title: Post-War Learning Environments: Redefining Schools Design in Iraq
Second Place Winner 2018
$1000 Cash Prize
Image (left to right): Tom Nixon, Sheb True, Michelle Miles, Stuart Romm, Phillip Tabb, Rana al-Rawi, Liz Martin-Malikian, Rick Fredlund and Tony Rizzuto. Photographer: Christine Vu
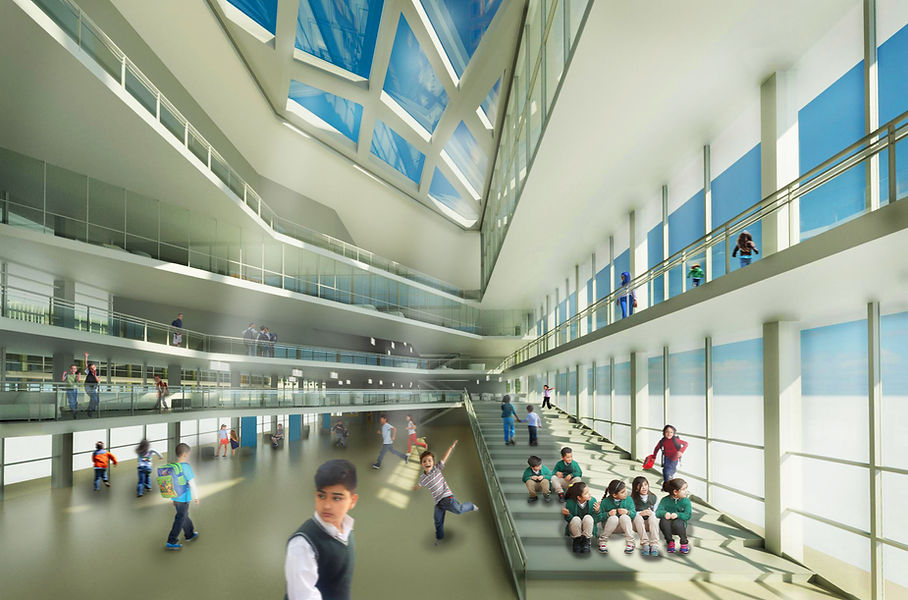
BUILT PROJECTS
Project Manager - Hiscutt & Associate

EBENEZER RETAIL
Rock Hill, South Carolina
8,500 SQ. FT COMMERCIAL BUILDING IN ROCK HIL, SC
Retail Project designed for Three tenants including Starbucks and Pacific Dental
Design started in 2018
Construction Completed in 2019
MARKET AT STANDING SPRINGS
Simpsonville, SC
This commercial project was designed to have a 48,000 SF Publix Supermarket Canopy along with 15,500 SF of shop space attached as well as an outparcel building with a drive-through.
Construction began November 2019 with an estimated project opening late 2020.

Construction for this Publix canopy along with 8 shops and an outparcel Starbucks building was completed in Nov 2020.
MAKOKO
Urban Design Studio
Professor Ameen Farooq
This project deals with a very challenging issues in the Makoko community. It is considered to be a unique community where the traditional slum site records the vernacular way of living on the water since it firstly emerged. It is facing a complete transformation congestion and overgrowth, water pollution from living and industrial waste,demolition and gentrification act proceeded by the government, etc.
The proposed Urban strategy uses the central node where the main water circulation intersect with each other creating a lot of traffic. The intention of this design is to reinforce the activity which occurs at this node by providing a better articulated ferry point with stalls on either side for informal trade to occur. The proposed structure will provide a market area and a community public space in the main first floor on the water level. The second floor will be an educational center with classrooms and a students gathering area take place. And finally, the third floor will be a walk-in clinic and a small pharmacy for the community. This development could be multiplied in each smaller districts following the same urban strategy.




4th Year Studio | Department of Architecture | Kennesaw State University
![]() | ![]() | ![]() | ![]() | ![]() |
---|---|---|---|---|
![]() | ![]() | ![]() | ![]() | ![]() |
![]() | ![]() | ![]() | ![]() | ![]() |
FLOWABLE CONCRETE SURFACE
Parametric Precast Concrete
School of Architecture | Georgia Institute of Technology
Fall 2019 | Professor Tristan Al-Haddad
The plastic nature of the concrete material is inherent to its fluid quality during the casting process. One of the primary characteristics of the material is its ‘flowability’ which allows the material to mate to its inverse, the form. The intent of the project is to design a privacy wall in precast adjacent to a swimming pool using the idea of ‘flow’ or ‘flowing’ as a conceptual departure. The pool is meant to ground the design in a simple, yet provocative and beautiful context. The project was also also an exploration in Physical Parametric Modeling using CNC Milling as well as using Urethane Formliners for the mold making to produce a 'mockup' concrete panel in a full scale.
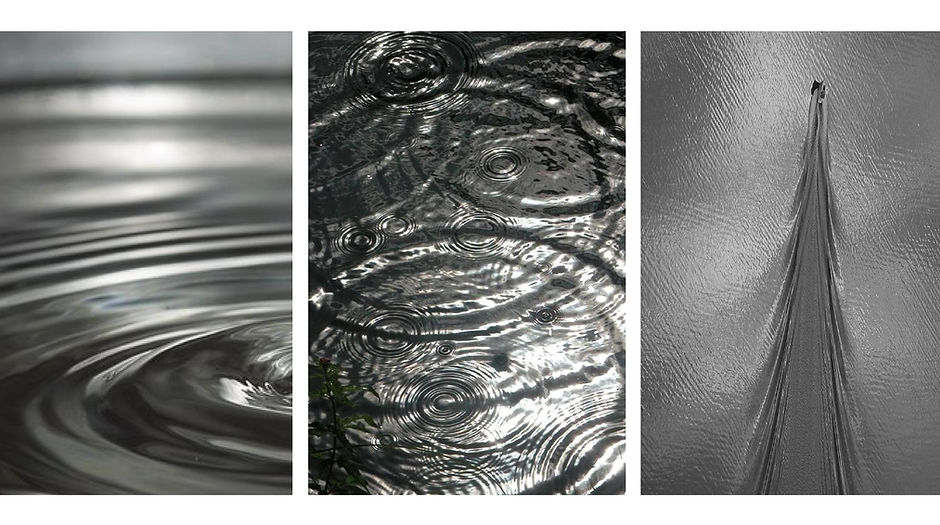
![]() | ![]() | ![]() | ![]() | ![]() |
---|---|---|---|---|
![]() | ![]() |
TWISTED CONCRETE LOUVERS
Parametric Precast II
School of Architecture | Georgia Institute of Technology
Spring 2020 | Professor Tristan Al-Haddad
Precast concrete louvers Design: Installation at the Georgia Institute of Technology Campus

![]() | ![]() | ![]() | ![]() | ![]() |
---|---|---|---|---|
![]() | ![]() | ![]() | ![]() | ![]() |
ISLAMIC GEOMETRIC PATTERNS
Shape Grammar
School of Architecture | Georgia Institute of Technology
SPRING 2022 | THANOS ECONOMOU, PHD
Shape Machine was used in this project, it is a new computational technology that brings shape-based search (⌘F) and shape-based replace capabilities (⌘R) to the geometric / vector modeling world for the first time.

![]() Rana Al Rawi - Final Project Shape Grammar _Fall 2019_Islamic Pattern_29 PAGES_Page_03.jpg | ![]() Rana Al Rawi - Final Project Shape Grammar _Fall 2019_Islamic Pattern_29 PAGES_Page_04.jpg | ![]() Rana Al Rawi - Final Project Shape Grammar _Fall 2019_Islamic Pattern_29 PAGES_Page_05.jpg |
---|---|---|
![]() Rana Al Rawi - Final Project Shape Grammar _Fall 2019_Islamic Pattern_29 PAGES_Page_06.jpg | ![]() Rana Al Rawi - Final Project Shape Grammar _Fall 2019_Islamic Pattern_29 PAGES_Page_07.jpg | ![]() Rana Al Rawi - Final Project Shape Grammar _Fall 2019_Islamic Pattern_29 PAGES_Page_08.jpg |
![]() Rana Al Rawi - Final Project Shape Grammar _Fall 2019_Islamic Pattern_29 PAGES_Page_09.jpg | ![]() Rana Al Rawi - Final Project Shape Grammar _Fall 2019_Islamic Pattern_29 PAGES_Page_10.jpg | ![]() Rana Al Rawi - Final Project Shape Grammar _Fall 2019_Islamic Pattern_29 PAGES_Page_11.jpg |
![]() Rana Al Rawi - Final Project Shape Grammar _Fall 2019_Islamic Pattern_29 PAGES_Page_12.jpg | ![]() Rana Al Rawi - Final Project Shape Grammar _Fall 2019_Islamic Pattern_29 PAGES_Page_13.jpg | ![]() Rana Al Rawi - Final Project Shape Grammar _Fall 2019_Islamic Pattern_29 PAGES_Page_14.jpg |
![]() Rana Al Rawi - Final Project Shape Grammar _Fall 2019_Islamic Pattern_29 PAGES_Page_15.jpg | ![]() Rana Al Rawi - Final Project Shape Grammar _Fall 2019_Islamic Pattern_29 PAGES_Page_16.jpg | ![]() Rana Al Rawi - Final Project Shape Grammar _Fall 2019_Islamic Pattern_29 PAGES_Page_17.jpg |
![]() Rana Al Rawi - Final Project Shape Grammar _Fall 2019_Islamic Pattern_29 PAGES_Page_18.jpg | ![]() Rana Al Rawi - Final Project Shape Grammar _Fall 2019_Islamic Pattern_29 PAGES_Page_19.jpg | ![]() Rana Al Rawi - Final Project Shape Grammar _Fall 2019_Islamic Pattern_29 PAGES_Page_20.jpg |
![]() Rana Al Rawi - Final Project Shape Grammar _Fall 2019_Islamic Pattern_29 PAGES_Page_21.jpg | ![]() Rana Al Rawi - Final Project Shape Grammar _Fall 2019_Islamic Pattern_29 PAGES_Page_22.jpg | ![]() Rana Al Rawi - Final Project Shape Grammar _Fall 2019_Islamic Pattern_29 PAGES_Page_23.jpg |
![]() Rana Al Rawi - Final Project Shape Grammar _Fall 2019_Islamic Pattern_29 PAGES_Page_24.jpg | ![]() Rana Al Rawi - Final Project Shape Grammar _Fall 2019_Islamic Pattern_29 PAGES_Page_25.jpg | ![]() Rana Al Rawi - Final Project Shape Grammar _Fall 2019_Islamic Pattern_29 PAGES_Page_26.jpg |
![]() Rana Al Rawi - Final Project Shape Grammar _Fall 2019_Islamic Pattern_29 PAGES_Page_27.jpg | ![]() Rana Al Rawi - Final Project Shape Grammar _Fall 2019_Islamic Pattern_29 PAGES_Page_29.jpg | ![]() Rana Al Rawi - Final Project Shape Grammar _Fall 2019_Islamic Pattern_29 PAGES_Page_28.jpg |
NEW PARADA
Media and Modeling II
School of Architecture | Georgia Institute of Technology
Fall 2020 | James Park
The Process of Studying the Prada Building In Tokyo
Project Team Members | Rana Al Rawi, Sandra Iskandar, Sookwang Lee
The Prada epicenter building is wrapped by a perfect Diagrid system that provides an enclosure envelope as well as external structure system to the building. To correctly model this system, we started by its analysis to find out that there were two main aspects that needed to be considered: First is the ratio within the single diamond module of the grid, each diamond has the ratio of x:y=3:2. Second is the relation between the grid and the building edges, where all the diamonds intersect and perfectly fit together when meeting at the building edges, producing a one continuous grid that perfectly wraps around the whole building. For this to be achieved, the grid must always start and end at the corners of each of the building faces, where each face must have an integer number of diamonds. In other words, the x dimension of the grid must always be a multiple of 3, and the z direction must always be a multiple of 2.
In order to achieve that, the method was to create 2 overlapping identical grids, where one is offset by half a diamond in the x and y directions. Both grids have 3 points for the x-step, and 2 points for the y-step, creating an ordered list of points. By trial and error, it was also discovered that the 2 grids must have equal number of rows equal number of columns, for the matriculation of points to work correctly. The logic is to join the ordered list of points from grid one with the ordered list of points from grid two.
Different order of starting points and directions were used to create the remaining lines in the diamonds.
One of the initial challenges for modeling the Prada building in grasshopper lies in finding the most convenient method for constructing its irregular geometric mass.
Since the architect provided the façade drawings as a series of surfaces connected together in a single flat foldable envelope, therefore it seemed more compatible to also model it in grasshopper the same way. Therefore, the process began with referencing the given unfolded building façade drawing in Rhino and then constructing points with x, y, and z coordinates in Grasshopper that represents the corners for each of the nine folded surfaces. Each surface had 3 or 4 predefined corners with one of its edges (or the crease lines) as the axis of rotation for that single face. Just like the way a sheet of paper can be folded, the parameters in this grasshopper algorithm was mainly controlled by the 3D rotational angles (0 to 360 degrees) in either straight vertical, diagonal or horizontal axes depending on the shape of that predefined face or surface.
What seemed to be the most significant factor about this method is the level of precision in the size and dimensions of modeling the existed building mass accurately, yet it doesn’t give the needed flexibility in controlling its parameters. In other words, it is possible to generate multiple of variations using these parameters like the fold angles or the size area for each of the surfaces, but it doesn’t guarantee that the result will be a closed folded envelope or volume for the building. Therefore, we needed to explore a different method in re-modeling the Prada 3D mass without losing the ability or the flexibility of producing multiple of functional design variations from its parameters.
Thus we started off with creating 5 vertices to construct 5 lines aligning from the base floor plan. On one condition when creating the vertices was the distance between each vertex which needs to be multiples of 3 due to the ratio of the diagrid system. Then the vertices are connected to create lines and divide the length of the line by 3 to get the precise integer only and orient the measured line by utilizing Circle component and Curve Closest Point component. When the 5 lines are created, extrude them to the height where it reaches the lowest part of the roof. This is to make the base façades of the building. The method in creating the roof is to continue extruding the lines from the lowest part and to the highest part of the roof. In other words, there is two separate extrusions, one creating the façades and one creating the roof portion. When the mass is created, make the angled surfaces to cut down the extrusion. The angled surfaces are made from the referencing lines of the edges of the mass. Extrude a line to a surface and offset to scale up the size of the surface. Angle them with the Rotate component and use the surfaces to split the extrusion. The roof is formed with 4 sloped surfaces which connect the edges of the extrusion. This defines as one edge to remain as an extruded surface from the bottom to the top of the roof. Of all the surfaces that forms the roof, the north oriented surface is rotated twice. In order to cut down the extrusion, the mass needs to be deconstructed and selected separately with List Item component to split with the surfaces by using Solid Difference component.
After the diagrid was created as 2D lines, it was taken as a merged pattern to be projected onto the 3D building mass. Since the building is a 5-sided polyhedral form, this process was a little complicated. The diagrid pattern was projected on each face separately, by 3D-rotating the pattern to be on a plane parallel to the surface and projecting it with a direction vector that is perpendicular to the surface being projected on. Once this process was repeated for the 9 different surfaces of the building, the output was a perfectly wrapped building by the diagrid pattern.
Then as part of our 3D-mass study, we explored some options to produce more variations from the original design by simply changing some of the parameters that we have defined within our algorithm. First, we changed the building footprint to regular pentagon, where each side is 12 meters, to maintain the diagrid proportions intact. The second variation was done by changing the parameter angles of the roof cutting planes and the building height, producing a much more dynamic and vibrant output. Lastly, we explored the option of simplifying the building geometry by changing the footprint into a square, again with maintaining the diagrid proportions, and playing a little more with the roof angles, thus producing 3 very different and interesting mass variations.
One of the most significant aspects of the project was the integration of the building façade and the building structure into a single designed framework. Since the diagrid system is the focal point of the project, the other systems follow that order accordingly by design including the structure components of the building that consist of the slabs and the vertical cores; however, the three cores locations are determined based on the structural framing plan of the slabs to be extruded vertically along the z- axis. The slabs are spaced out based on the height of two diagrid modules where the boundary of each slabs takes the shape of the building geometric mass. Structurally, these slabs transfer the weight from that diagrid façade system to the cores of the building. The 3 generated design variations for the structural system complement the 3 design variation for the building envelope while it varies in the sizes and dimensions of the cores as well as the height between each of the building floors.
The horizontal cores are made based on the diagrids that are utilized as envelopes of the building structure. Where the intersection of the diagrids and the second, fourth, fifth level slabs meet are the pivots for each horizontal cores. Brep Curve component is used to find the intersecting vertexes, and List Item component is used to distinguish the centroid of the core. From the centroid, the left intersecting vertex becomes the left corner of the diamond core, in which the right intersecting vertex becomes the right corner of the diamond core. The top and the bottom vertexes are also the top and bottom points from the centroid which makes the size of 4 diamonds put together. From getting the four vertexes on the other side of the façade, the two facing diamonds are connected by creating horizontal surfaces and making them as solids by joining and capping. These surfaces are offsetted to create the thickness by 0.
Lastly, each corners have been rounded by using the FilletEdge component with the radius of 0.3.
RECLAIMING A LOST LEGACY
Georgia Institute of Technology Demonstration Project Category EPA Rainworks Challenge 2020
Prepared with support by:
Jason Gregory, Senior Educational Facilities Planner
Dr. Richard Dagenhart, Associate Professor Emeritus of Architecture & Urban Design Haythem Shata,
Design Engineer (Sherwood Design Engineers)
Project Team Members | Simran Bajaj, Rana Al Rawi, Luben Raytchev, Christopher Tromp